Our construction safety mission
At GMS and across our family of companies, safety isn’t just a priority—it’s our mission. We are unwavering in our commitment to creating a secure work environment where employees, contractors and customers are always protected. Our ultimate goal is zero accidents, ensuring everyone returns home safely each day.
To achieve this, we strictly adhere to safety regulations, actively eliminate hazards, raise safety awareness, provide top-tier protective equipment, and deliver comprehensive training and education. Backed by our Board of Directors, our management team champions a culture of shared responsibility built on collaboration, best practices and the open exchange of ideas. Together, we’re relentless in our efforts to uphold the highest standards of safety for everyone we serve.
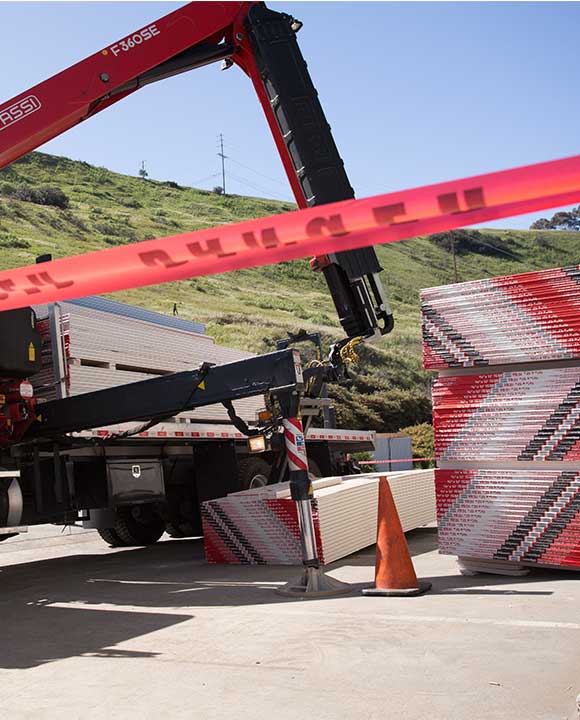
We believe preparation and training are key elements to ensuring job site safety for our people and others, both on and off the job site. Each subsidiary trains and certifies all of its operators in-house so they are prepared to safely perform their job, whether it’s managing materials in the warehouse or delivering materials to the local construction job site. Local safety managers oversee vehicle maintenance, direct safety reviews and implement weekly safety meetings providing continuous safety training on articulating boom loaders, fall protection, hazard communication, materials handling and more. GMS is a drug-free workplace, which goes hand-in-hand with our safety culture.
A few highlights from our comprehensive safety training and communication program are:
Gypsum Management & Supply University (GMSU) – a cloud-based online training warehouse providing timely safety curriculum.
RISKTalks – an innovative approach to weekly safety meetings covering industry-related topics, while encouraging dialogue, participation, and feedback from all participants.
Safety In Action – enterprise-wide safety communication platform designed to inform team members of safety-related topics which may affect them or require prompt attention.
Accident Bulletins – quarterly communications highlighting accidents / injuries along with root cause analysis intended to prevent future accidents.
Boom Crane Simulator – a virtual reality-based training program providing new operators with basic training without the exposure of potential accidents.
We strive to provide the highest level of safety not only for our crew, but for your crew, other delivery partners and people on the construction job site. Prior to delivery to your job site, we conduct pre-delivery reviews documenting specific requirements and safety considerations. Post-delivery, we conduct job site reviews to ensure our crew delivered to our high standards. We are fully committed to regulatory compliance under OSHA and DOT.
We have a comprehensive Risk and Safety team, including dedicated and certified safety managers across our businesses. We continuously educate ourselves and implement and uphold all rules and regulations from regulatory bodies applicable to our business. In addition, we work to continually develop and evolve our safety programs and tools to support and protect our employees. A few examples are:
Collision Avoidance Technology: all new vehicles are outfitted with collision avoidance technology.
Truck cameras: we are in the process of retrofitting all logistics vehicles with driver, forward, rear, and side-facing camera systems. All new vehicles procured are equipped with these cameras.
Driver Scorecard: a grassroots tool combining four main sources of both lagging and leading indicators to assess driver qualification and performance.
DriversAlert: a safety decal – based program allowing for third party notification of both positive and negative driving behaviors. Decals are included on all delivery trucks and trailers.
Vehicle Fall Protection: custom reusable tarps and establishment of a safety policy to mitigate the risk of falls from our trucks.
Cable Viper™: internally developed and patented a tool to unlatch railcar cabling without the need for an employee to be on top of a rail car which eliminates fall hazards.
Safety Task Force: Safety products, including PPE, that have been tested internally by our employees to ensure quality and protection.
Our safety program can only improve and develop through comprehensive data capture and analysis. We have implemented programs and processes, such as:
Integrated Risk Management (IRM): a risk management information system which allows us to accurately and frequently analyze our injury and accident trends and exposures.
FieldID: a cloud-based application allowing us to uniformly create audits, observations, and inspections, including Monthly Operating Risk Assessments, Annual Internal Risk and Safety Assessment, and pre- and post- delivery job site inspections.
Safety Perception Survey: enterprise-wide survey to measure our employee’s perception of the effectiveness of our safety program.
Standardized Metrics and KPIs: monthly and quarterly metrics detailing enterprise-wide performance trends from a frequency and severity perspective.
1,000 Day Injury-Free Recognition: celebrating locations with 1,000+ injury-free workdays.
Consistency across geographies
With GMS, you don’t have to worry about safety from site to site and region to region, our safety protocols are the highest in the industry with network wide training for optimal and consistent implementation. We employ a regional network of safety managers who work closely with dedicated safety professionals at our subsidiaries. These regional managers develop training curriculums, advise on latest changes in OSHA and DOT compliance, share best practices, and ensure that all GMS locations adhere to the same high level of safety protocols. GMS implements the latest technology to ensure uniformity in the way our safety standards are measured. Our inspections, audits, and observations are in tandem with regulatory requirements and are some of the most comprehensive in the industry.
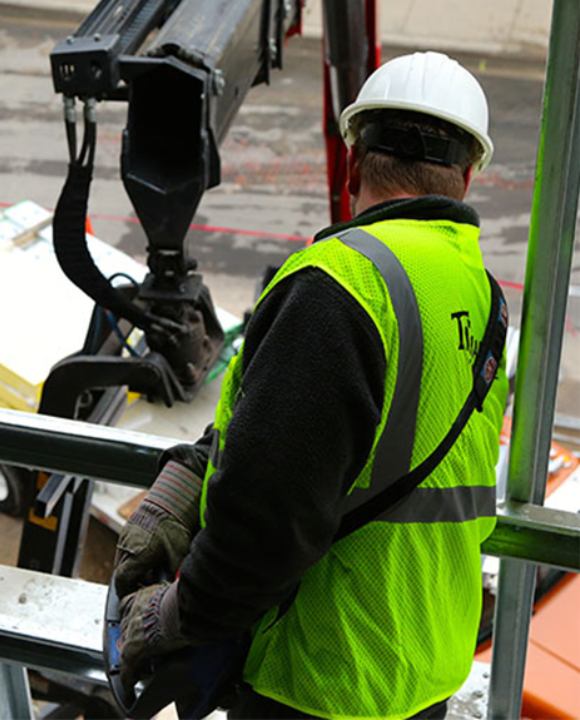
It’s easy to get in touch with us. We’re your neighbors, and we’re here to help. Give us a call, drop by, or send us an email and let’s talk.